Implementation of the company's acquisition process by merging and integrating systems
- FMCG
- Worldwide
- SAP and others
- 3-14 months
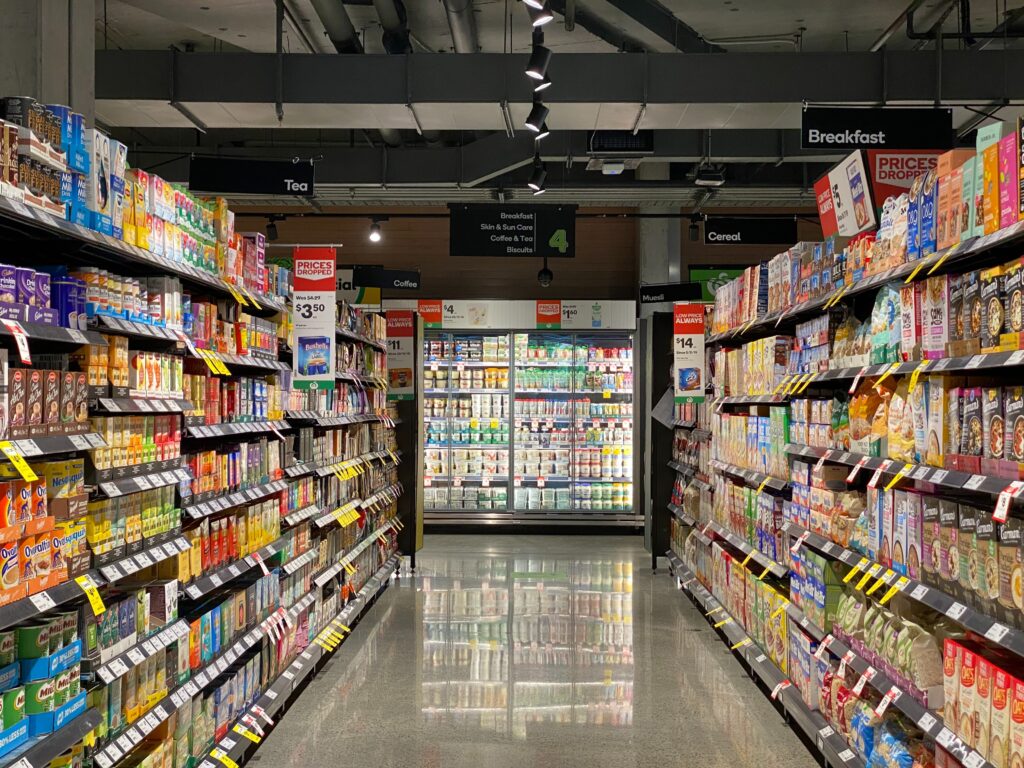
Overview
The company is one of the biggest in the FMCG Industry with worldwide range and multiple, well known brands, specializing in the production of fast-moving consumer goods.
Our Client bought a company which was using their own SAP system not only for sales, but fully enhanced production including all possible productive areas like production planning, inbound/outbound logistics, finance, controlling and quality.
Challenge
The biggest challenge of the acquisition and developed merger plan was to have one common central system to support the integrated business operations of the companies, including areas like: Master data, Customer Service, Sales/Merchandising/Digital, Physical Logistics/Q&FS /Co-packing, IT Integration/Infrastructure, Demand Forecast /CRP, S&F + Corporate reporting, P&O/Legal, Commercial.
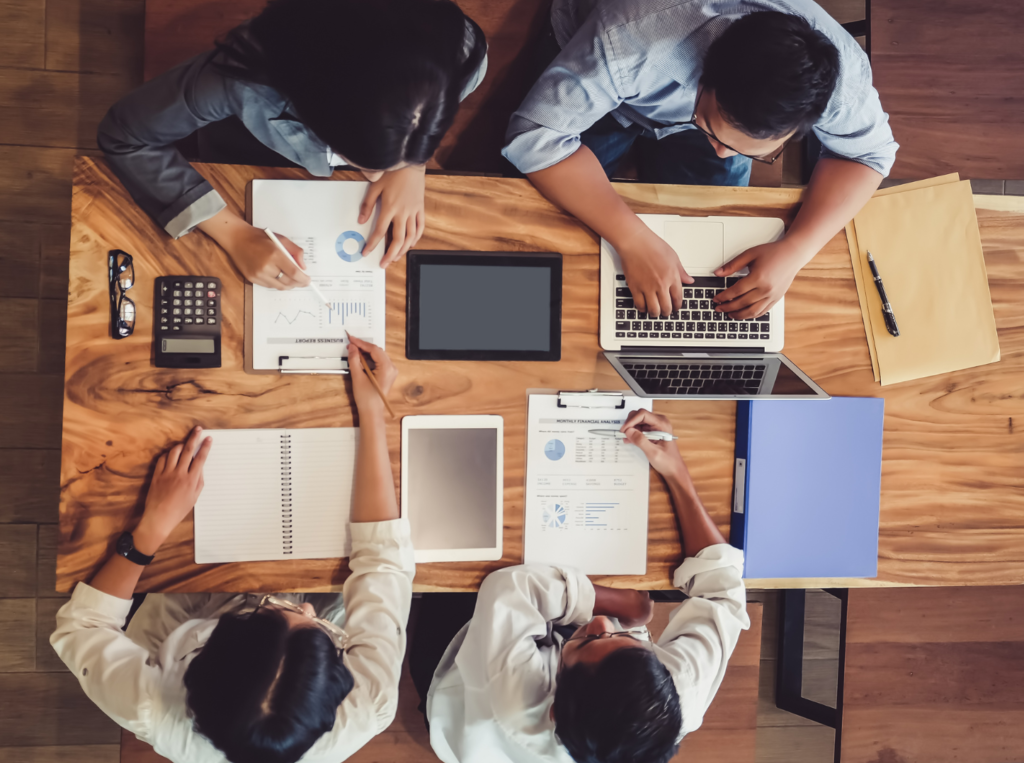
Solution
Initially, after the acquisition of the company, the decision was made to maintain production in the “old” system while transitioning all markets to the new owner’s SAP environment. The two landscapes differed in terms of release levels, maintenance strategies, and template approaches. Additionally, a few automated processes, often referred to as “robots,” were implemented to validate data accuracy between the two systems. This approach significantly streamlined and optimized the transition process. Mergers and acquisitions of companies are complex processes, requiring appropriate specialized background and implementation of solutions adequate to the requirements and goals of a given company.
Both Companies integration has been in progress since 2017. The primary intent of the acquiring company was to integrate the demand or market functions of the business only. At first 16 EU market-countries has been transferred to the new system.
At the start of the global program, on the business level, conversion of the bought factories from “old” SAP to another SAP was not considered a necessity.
In late 2018 a pilot program where 3 factories were approved to understand cost, benefits and determine the viability of converting a factory to SAP.
Philippines (live Jul ‘20), the US (live Aug ’20) and the UK (live Apr ‘21) selected as the pilot factories.
The Enterprise Architecture team determined that moving to S/4 (next generation SAP) in the future would be easier moving from 1 ERP solution. Factory conversion was a complex program with only 40% of the activity in ERP. The remainder are all the peripheral systems for product design and execution (Radar, Supply Planning, Scheduling, Veritas, Keystone, T&C, CFIN, Internal WH, Factory Dispatch).
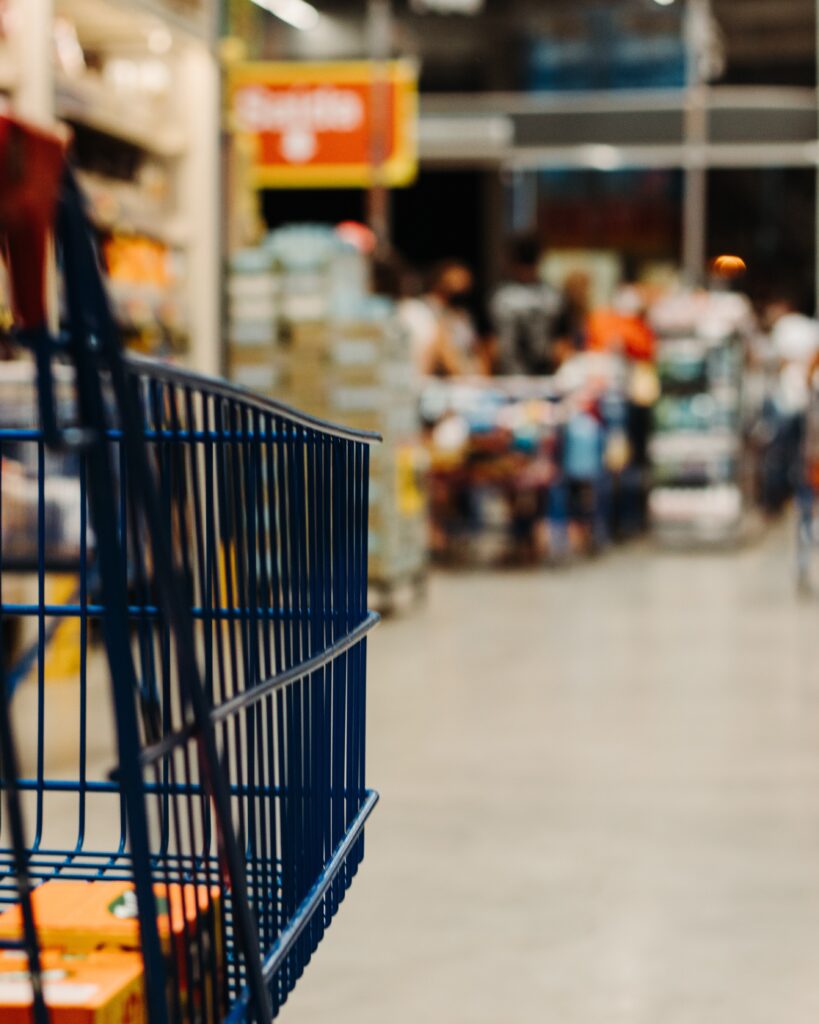
Results/Benefits
With the successful integration and conversion of the factory, the acquiring company achieved a number of hard and soft benefits, including:
Tangible hard savings:
- finance period close efficiency and synergies with legacy choc factories & MFS, remove complexity of Hybrid process (SAP1 <>SAP2 processes);
- pallets distribution labelling system implementation will streamline the dispatch of multiple DC’s in exports markets;
- inbound planning teams : synergies through single systems.
Cost avoidance:
- harmonize landscape : further supply enhancements and future project cost avoidance (inbound traceability + project cost avoidance);
- easter Europe factory: cost avoidance loss in case of non-having AEO status (certified std organization issued by customs admin. in EU).
The below cost savings are for “old” SAP system:
- energy (power & cooling);
- network charges;
- backup licenses;
- system licenses;
- physical server;
- storage.
Large number of benefits of migration to one ERP that don’t cause tangible savings, but significantly reduce business risks and drive efficiencies:
- prevention of a large business disruption if something goes wrong in “old” SAP due to the loss of knowledge;
- governance and control : the simplification of business process and control from 2 systems to one will significantly reduce the risk of error and non-compliance;
- allows for a simpler future transition into S/4 HANA;
- deployment of Global Traceability standard : traceability improvement, hold & release integration. Automation of recalls to comply with 4 hour standard recall window, cost avoidance of overhead increase. Deployment of Testing & Conformance tools that are mandated by the global Traceability Transformation Program;
- lack of “old” SAP Process Knowledge : benefit from consolidation of regional functional experts & key users community. Would mitigate long term Controls & Compliance risks, promote standardization and automation of close processes;
- drive further efficiencies in shared services with MCS, MGS-F, DT service team;
- allows all factories to be 100% comparable, lowering risk for reconciliation issues;
- digital tool development will be much more efficient and cost effective as they will only be required for one system. Also any deployment of new systems will only need to happen once, saving on development, testing and deployment resources;
- efficiency of stock control within a single system will lead to a reduction in finished goods stock holdings;
- improved Data management throughout the manufacturing process using one common harmonized product identity without the current conversion between factories;
- improved management of raws and packs with common commercial contracts and aligned ways of working with vendors;
- common costing model : provide Production Conversion Cost clarity between all factories in the region;
- streamline tax reporting process with Factory and Market under the same LE;
- SAP T&C process linking with batch management replacing manual process;
- structure BOM in managing material changes;
- traceability solution for rework;
- remove multiple manual entries of the Recipe/BOM data;
- harmonized organization driven by a common solution.
Average implementation period was reduced thanks to few dedicated teams which not only shared the knowledge between them and overlapped projects, but also shared lessons learned, tricks and tips and communications between each other. The fastest rollout was done only in 3 months, while the biggest factories like the UK took us no more than 14 months.
Here you will find expert support on SAP
See other case studies
Discover our capabilities
19+ years of experience
Since 2006 we have been helping our clients implement and develop systems and applications that streamline business processes. Owing to our know-how, our Partners are able to fully utilize the technologies of the future.
1000+ completed projects
We approach each project individually. We employ technologies that improve the enterprise functioning and management. The joint implementation of each projects brings our clients closer to perfection in managing a modern organization.
450+ employees
We have an appropriate team of experiences and qualified experts in many fields. Consultants, analysts, programmers and PMs. We have been successfully implementing even the most complex projects that streamline the development of organizations around the world.
50+ countries where we have carried out deployments
Based on our unique skills, we implement innovative projects around the world. We conquer new markets and constantly enter new areas. A comprehensive approach allows us to ensure the development of companies from numerous industries and sectors.
Contact us!
Let’s talk! Are you interested in our solutions? Our experts are happy to answer all of your questions.