ERP systems data merging with a robotics solution
- Large International FMCG Company
- Retail
- Global
- SAP
- 5 months
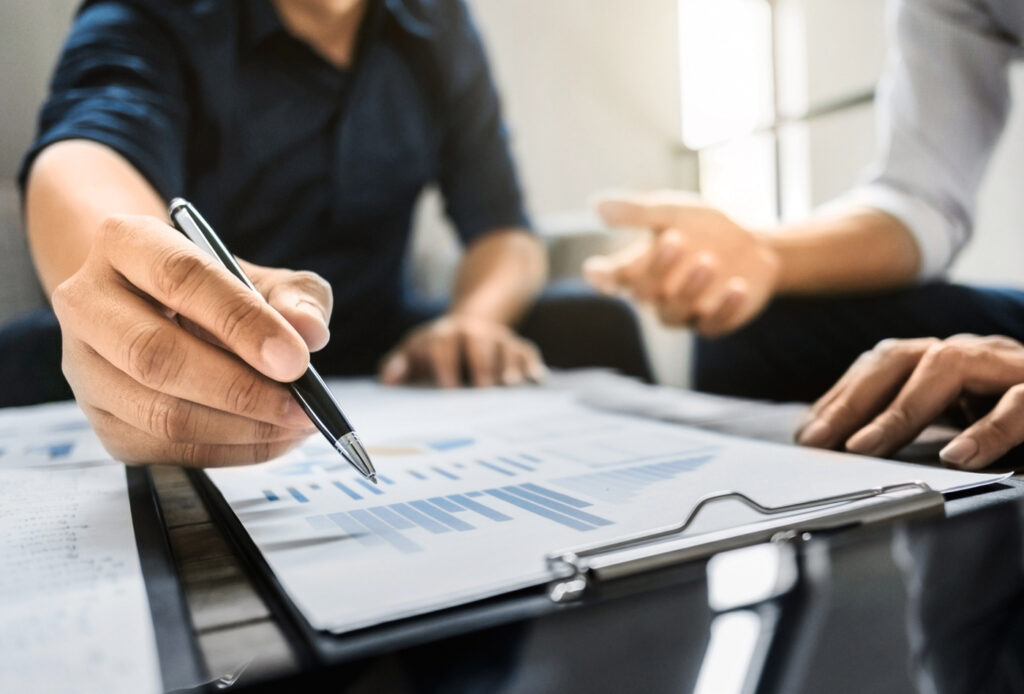
Overview
Merge & Acquisition of a company with leverage the new integrated stock transfer process development to ensure completeness and accuracy of data being transferred between the ERP systems.
In today’s world merge and acquisition of companies is a common way to gain financial benefits following their strategy for sustained growth
and market expansion. Operating reorganization might be a huge challenge due to natural systems differences, various releases, business habits
and maintenance level.
Background
Taking into account the potential benefits and risks from the reorganization, we consider the following operational company merge approach:
- Transfer to (non)SAP solution of one the parties,
- Joint-system solution with a combination of both.
While the first solution seems to be obvious then what if we need to combine two separate, operating SAP systems? Below, you’ll find out how we confronted that challenge and solved our client’s problem.
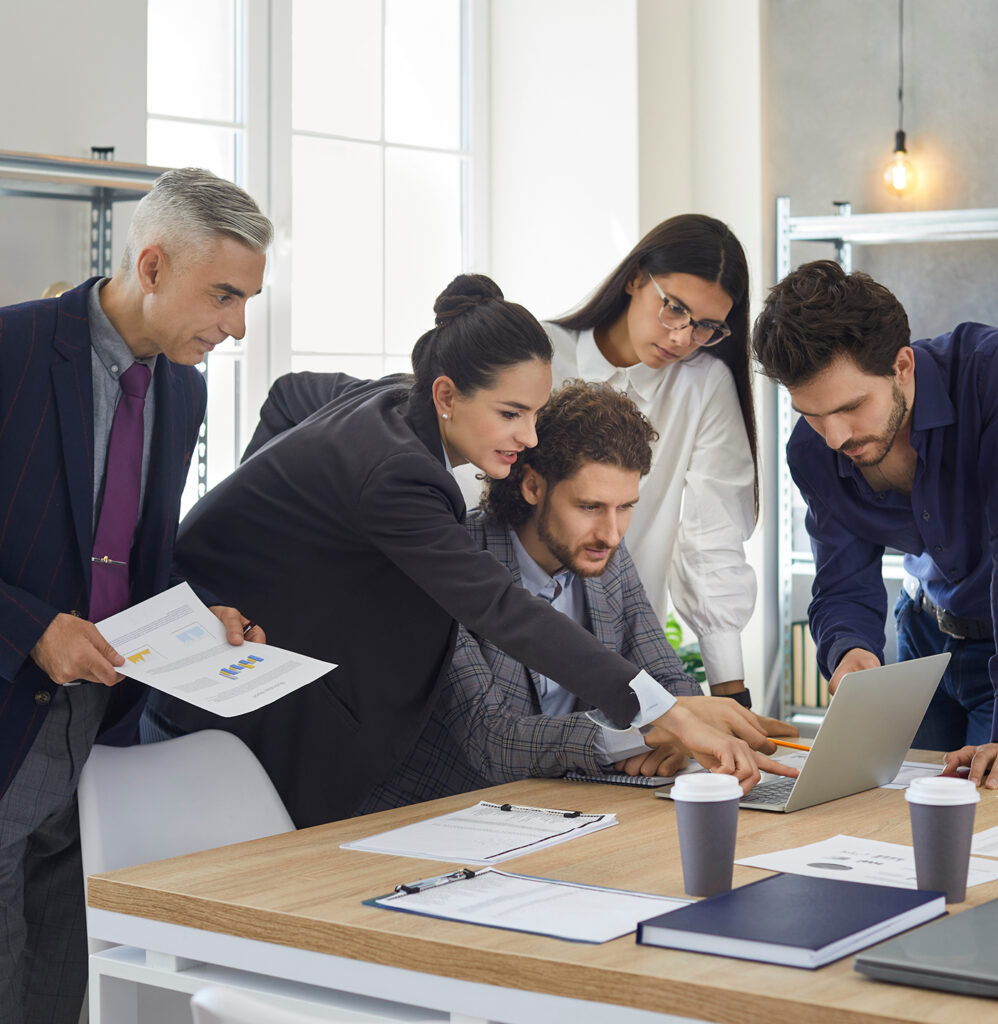
Challenge/Problem
Few years ago, our client bought a company which was using their own SAP system not only for sales, but fully enhanced production including all possible productive areas like production planning, inbound/outbound logistics, finance, controlling and quality. Once done – our client asked for one simple solution to keep the factories in the “old” system and move all market units into his own system.
The transformation program globally required to combine company A and company B business units into combined legal entities with a new company A name. Historically, company A units were running SAP system (A), and company B units are running SAP system (B). Transformation program scope included running all market business operations in the (A) system, while factory business operations will still be running in the (B) system. This would mean that the integrated factory-to-market process will be running in two systems and inventory will need to pass from one system (B) to the other (A).
Expected benefits:
- Drive standardization, optimization and increase efficiencies via retirement of multiple company B legacy made-to-measure programs and elimination of manual adjustments in system (A),
- Standardization of intra-unit process across both systems,
- Ensuring transactional integrity of material prices,
- Leading to a better data accuracy,
- Identified robotic options to improve efficiency & user centricity,
- Avoid long-term inconsistency,
- Ensuring COPA reporting accuracy.

Solution
Leverage the new integrated stock transfer process development to ensure completeness and accuracy of data being transferred between the ERP systems, ultimately optimize Intra-Unit and Inter-Company Process to support company A globally via the hybrid model.
Finance statements, reporting and interfaces as well as reconciliation for period close processes were developed and aligned country specific gaps with global best practice to drive standard approach for factories and markets. Facilitate, both, cost and growth value unlock for the combined company A and company B segments.
Each of implemented solutions has great importance to the work of the project, however, solutions used robots were crucial:
- Since factory is operating in SAP (B) and market plants are placed in SAP (A), costing is done in each system separately. To avoid differences, there is a need to monitor this on a period basis.
- Since a new integrated stock transfer process is being developed for which, we require a report to ensure the completeness and accuracy of data being transferred between systems and ultimately the financial statements of the units involved.
- To create a report/tool that will compare COPA summarization tables data between SAP (B) and (A) after sales data transfer between the systems.
What is a robot?
- Robot is an automated process which is validating data accuracy between SAP (B) and SAP (A).
- Robot works on a virtual machine, that in not accessible by any users. With that, users are not able to see any steps performed by the robot in the background.
- Robot is verifying data accuracy for an agreed process and send a list of mismatches (reconciliation report) to an agreed address by email.
- End user(s) need(s) to review the output generated report in order to analyze all possible reasons why processed
and displayed data differ between both SAP systems.
Processes which are covered by robots:
- Standard Cost Reconciliation,
- Intercompany Price Reconciliation,
- (A) system to (B) system Retrofit Reconciliation.
Benefits
- Comparison reports created automatically
- All found difference send to users based on the predefined table
- Separate reports for each Country in the scope
- No risk of mistake between systems
- Short time of creating reports
- Possibility to run report ad-hoc (i.e., when new material will be created or after fix)
- Easy communication with Robot (via mail)
- Confidential data additional security approach
- Flexible solution (easy way to add new country to the process)
- User-friendly guidance-book
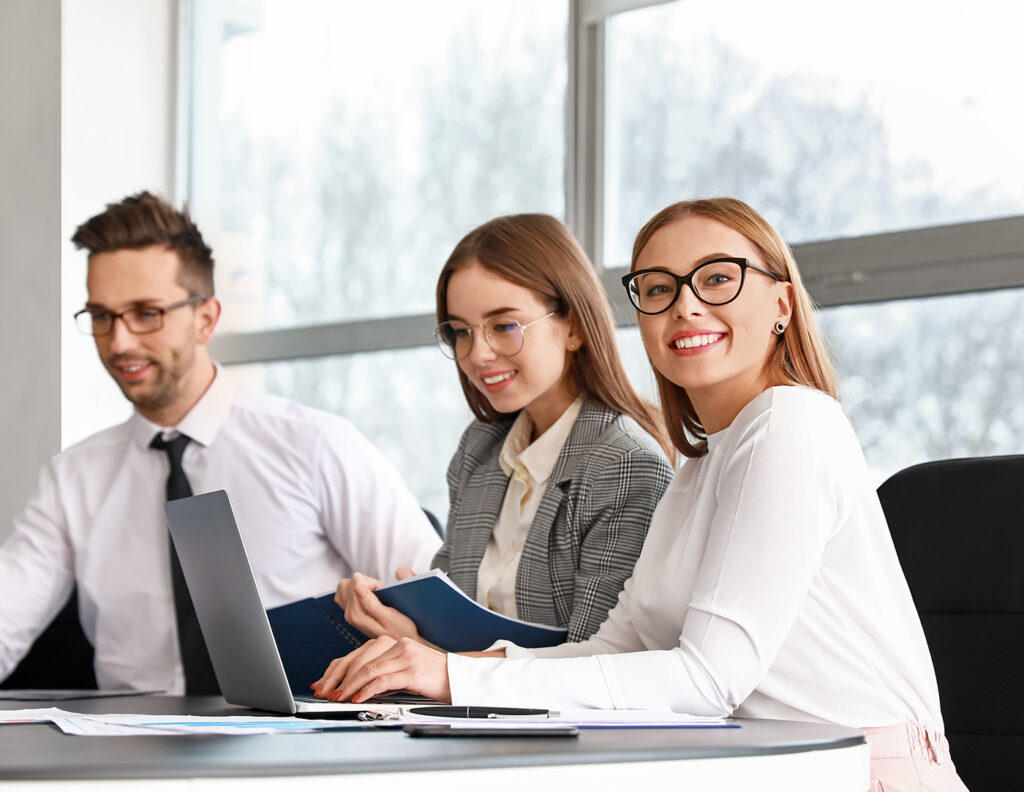
What have we learned?
We dealt with many areas during the project, so that it was incredibly developing experience for us. At that time, we faced, among others:
- Sales of products from (B) factories to (A) markets,
- Transfer of goods inventory between factory to market within same legal entity,
- Intra-Company Cost Transfer within same legal entity,
- Sales Retrofit of 3rd party sales volume from (A) system to (B),
- Automated factory revenue recognition for intra-unit shipments,
- Inter Company Business Logistic Cost Handling (Russia),
- Multiple Sourcing/ePlant (China & US).
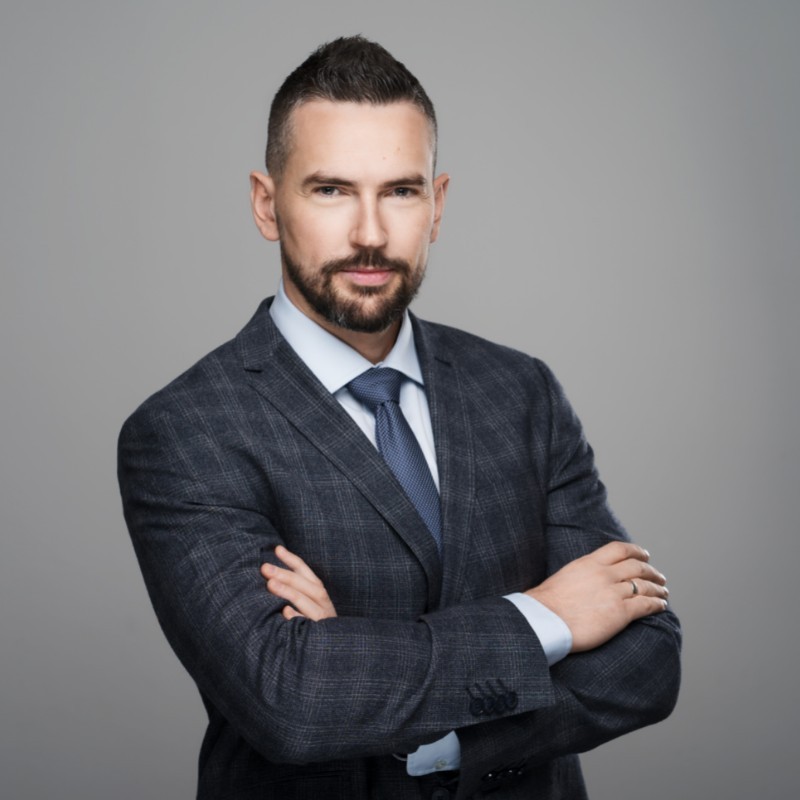
We are glad that thanks to an innovative approach, we were able to help our client connect data in two SAP systems in real-time and take care of the integrated transfer process. This solution certainly translates into increased work efficiency and stable growth consequently. Working on the project was a really developing experience for us. Considering the complexity of this project, our team had a chance to prove themselves in many SAP areas. In particular, the implementation of robots is another confirmation of how important automation is in today’s world.
Here you will find expert support on SAP
See other case studies
Replication of MRP Areas between SAP MDG and SAP ECC
Implementation of the ERP system enova365 in many companies of the Opolgraf brand
Implementation of the company’s acquisition process by merging and integrating systems
Report optimization in the FMCG industry
Discover our capabilities
19+ years of experience
Since 2006 we have been helping our clients implement and develop systems and applications that streamline business processes. Owing to our know-how, our Partners are able to fully utilize the technologies of the future.
1000+ completed projects
We approach each project individually. We employ technologies that improve the enterprise functioning and management. The joint implementation of each projects brings our clients closer to perfection in managing a modern organization.
450+ employees
We have an appropriate team of experiences and qualified experts in many fields. Consultants, analysts, programmers and PMs. We have been successfully implementing even the most complex projects that streamline the development of organizations around the world.
50+ countries where we have carried out deployments
Based on our unique skills, we implement innovative projects around the world. We conquer new markets and constantly enter new areas. A comprehensive approach allows us to ensure the development of companies from numerous industries and sectors.
Contact us!
Let’s talk! Are you interested in our solutions? Our experts are happy to answer all of your questions.